Conventional nuclear thermal rockets such as the NERVA can have a specific impulse of around 900 seconds, about twice what you can get from conventional chemical rocket engines. That’s good, but it’s also really low compared to what could be obtained from nuclear thermal systems. Solid core NTR’s have core temperatures substantially cooler than what you’d see in, say, an SSME, and for good reason: the core would soften and fail if it got much hotter. Thus the reason for the high performance of NTR’s is not due to high temperature, but to low molecular weight of the propellant (pure hydrogen, rather than water vapor for the SSME). But what if the core wasn’t limited to the low temperature of an NTR?
One way to do that is the gas-core engine. Here the uranium is allowed to not only melt, but to vaporize. It it retrained in the engine, typically, by spinning the engine or at leas the vapor. Thus the dense uranium vapor is spun out to the walls of the engine, and the much lighter hydrogen propellant is in the core. The keep the walls of the engine from melting, the hydrogen is first released into the engine from the walls themselves. The hydrogen bubbles up through the seething uranium gas, taking heat from the uranium as it does so.
Another approach is illustrated below, the Coaxial Flow Gaseous Nuclear Rocket. Here, instead of uranium spun to the walls, vaporized plutonium is retained along the centerline of the engine, with hydrogen flowing around it.
In these cases, specific impulses can get in the range of 5,000 seconds. But the problems with these designs were many. Startup and shutdown would have been lengthy and complicated processes. In the best cases, some of the fissionable gas would have escaped, meaning excess would need to be carried. In the coaxial system, it’s not entirely clear just *how* the hydrogen was to keep the plutonium vapor in place.
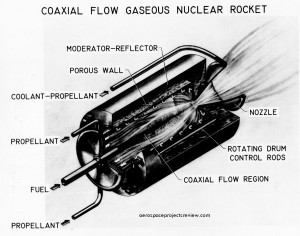